A Comprehensive Guide to the STL File Format
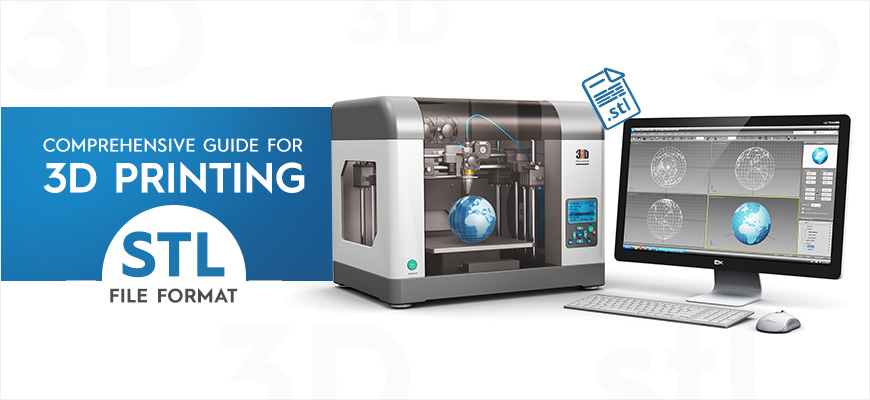
Struggling with low quality 3D printing of STL files? Disappointed with the formation of large files during the process. Nothing to worry about. This blog is exclusively carved for you to take you through the detailed understanding of STL file types and its process of exporting and printing formats.
What is an STL file format?
The STL is a file format that represents a 3D object's surface geometry using a collection of triangles. It does not store any details about color, texture, or any other attributes. An STL file format is a common format used for 3D printing designed by CAD software. STL is the acronym for stereolithography and stores the information of a 3D model. It shows the unstructured, raw, and triangulated surface geometry of a digital model without any CAD attributes like color, materials, textures, or line styles. The number of triangles increases with the complexity level of the 3D model.
Standard Triangle Language, commonly abbreviated as STL is the preferred and reliable option for the 3D printing purposes. The whole concept is based on the sequence opf triangles that make up the surface of the model. It is also worthwhile to note that the CAD formats allow easy conversion to STL files for a quick and easy printing process. The process of conversion of 3D models into STL formats makes them ready to print.
Methods of Exporting STL Files
Please take a look at the steps below to clearly understand how you can make your STL files print-ready! By doing so, you can reduce the costs incurred for 3D printing.
-
Have the proper idea on STL resolution
STL utilizes the sequence of triangles that make up the surface of the model. When the count of triangles is increased, so does the resolution which would result in good results. However it will increase the size of the file for 3D printing.
In case of low resolution, the triangles would be seen on the model surface after printing. For sure, you would not prefer this. But this would help you to enhance the digital look and feel with the low poly models.
So, understanding the right image resolution is really important. Let’s also understand that minute details will be difficult to capture. Because if the file size is increased, it will adversely affect the print design.
-
Key note on the export parameters
STL files give you the flexibility you need in terms of resolution. The most preferred tolerance level adjustment is to set it high when you are looking to make STL files that can seamlessly get printed. STL parameters to be kept in mind include: Angle and the height of the chord that gives you the actual distance between the CAd surface and the newly formed 3D print surface. The ideal chord height includes 1/20th as that of the size of the printing surface.
Please note that you should never set the chord length below 1 micron because if its too low, then it would even affect the quality of the 3D print design.
When we say the angular tolerance, it generally refers to the angle between the adjacent triangles. By default, its value would be 15 degrees. The higher the value you set, the smoother the surface will be.
-
Cad software is a must have to export STL files
Once you have the Files ready, what’s the best way to export it? Of course, by using the CAD software. The process may seem unique for different platforms. Hence it is necessary to rely on the standardized mode to be efficient.
Hoep, the major factors that we have covered in this blog would help you in getting a proper understanding of how better you can utilize the STL files for your 3D print designs. Apart from the above, some more important aspects that you would need to consider include:
- Maintain the chord height upto 0.001 mm.
- Thumb rule is to maintain the tolerance angle to a maximum of 15 degrees.
- Never try to export the CAD file to STP format in case you feel the file size is too large.
By keeping these points in mind for your 3D print designs online, you can succeed with the affordable ways of printing 3D jewels, healthcare equipment or anything else. The best way is to outsource to a service provider who can make it easy for you. It is however obvious that you may find a good number of 3D printing companies that would help you with the best 3D print design services.
Related Article : 52 Free CAD Software That You Can Use in 2025
Special Rules for the STL File Format
Here are some special rules that apply to the STL file format, which you should know about:
The Vertex Rule
According to this rule, every triangle should share two vertices with the adjacent triangles. This rule should be followed during the tessellation of a 3D object’s surface.
-
The Orientation Rule
This rule suggests that the orientation of a 3D object’s facet should get defined in two ways. The first rule states that the normal should point to the outer side. According to the second rule, which is also referred to as the right-hand rule, the vertices get listed in the counterclockwise direction. This rule guarantees data consistency.
-
The All Positive Octant Rule
This rule states that the coordinates of the vertices of the triangles should all be positive. This translates into the fact that the 3D object would remain in the 3D Cartesian System’s all-positive octant. The rule is meant to save space; if 3D objects are made to remain at any place in the coordinate space, professionals would have to deal with negative coordinates.
-
The Triangle Sorting Rule
According to this rule, the triangles need to appear in the rising z-value order. This rule facilitates faster slicing of 3D models.
How to Optimize STL Files
The STL file format replicates a CAD model’s surface to some extent using triangles. However, this is never perfect and the facets give the model a degree of coarseness. A 3D object having the same degree of coarseness as the STL file would get generated. However, if you go on decreasing the size of the triangles, you can improve the approximation and the print-quality at the same time. When you decrease the triangle-size, you would need more triangles to cover the entire surface. This would create massive STL files that most slicer would fail to process. Such huge files would also be difficult for you to upload. So you should know how to strike a proper balance between print-quality and file size. In some CAD software, you would come across certain settings while getting your STL files exported. Such settings determine the facet-size, file-size, and even the print-quality.
STL File Alternatives
Notably, the STL format is not the only 3D print-ready format; more than 30 3D printing file formats have been invented. OBJ is a widely-used file format, which can keep texture and color profiles saved. PLY is another format that is used to save scanned 3D objects. Off late, The 3MF Consortium is looking to introduce a new file format called the 3MF format . It is expected that this file format would make the 3D printing process more efficient.
Difference Between STL and Other File Formats
-
STL and OBJ
The STL file is most prevalent in 3D printing and is used to save geometry. It encodes the geometry of the 3D models that contain triangular meshes. STL files don't compute information like color and texture. In comparison, OBJ file format is most commonly used for 3D scanning. It represents the different polygons that are in the same file and supports the surface encoding. It has a great representation of color, size, and textures.
-
STL and 3MF
STL files are basically unstructured and trained surfaces that do not contain color or material information. It describes only the surface geometry of a three-dimensional object. In addition, it requires reslicing to edit the geometry. In contrast, 3MF files are an XML-based format containing all the information you need to print a model. It includes data like textures, materials, colors, and mesh. Here the models are positioned without reslicing.
-
STL and gcode
The STL file format represents the 3D models and is used for 3D printing. With the help of a 3D slicer software program, it communicates with the printer to print the model. Today, it is widely used in rapid prototyping, 3D printing, and CAD manufacturing.
In comparison, the G-code file format is the programming language instructing the printer what to do. This includes printer nozzles, extruder temperature, pauses, printer head speed, etc. It is widely used in cutting machines like lathes and mills. STL file formats need the slicer to slice into layers, whereas you can view the layers on your computer using G-code.
-
STL and STEP
he STL file only describes the 3D model's surface geometry and contains the triangular mesh, but the STEP file saves the models as single entities, requiring higher accuracy and smoother curves. STEP files are best suited when you want an accurate model, curved parts, or machining parts. If you plan to do lots of editing after exporting, then consider using STEP files.
If you want to create 3D printed models that don't require high-fidelity prototypes and do not require editing, then you can use an STL file. As a result, STL files are simpler and more efficient than STEP files.
Conclusion
Different 3D file formats find use in different industries. Through this article, we have jotted down the list of the 10 most popularly used file formats for different industries. STL is still the most widely used 3D file format among the mentioned names.
Always remember to choose the file format according to the intent of the 3D file, as knowing the project's intent will solve most of your problems. Additionally, the platform where your final work will be published and if the 3D file format you pick is compatible with the software you are using are things to keep in mind too.
Click on the alphabetical dropdown menu to know the names of more 3D file formats.
Hope this article will come handy to all who are seeking the names of the popular 3D file formats. Stay tuned for more such pieces, and keep increasing your knowledge base!
If you want any Customized 3D modeling solutions, we are just a click away
Contact Us