Top Things You Should Know About Surface Modeling
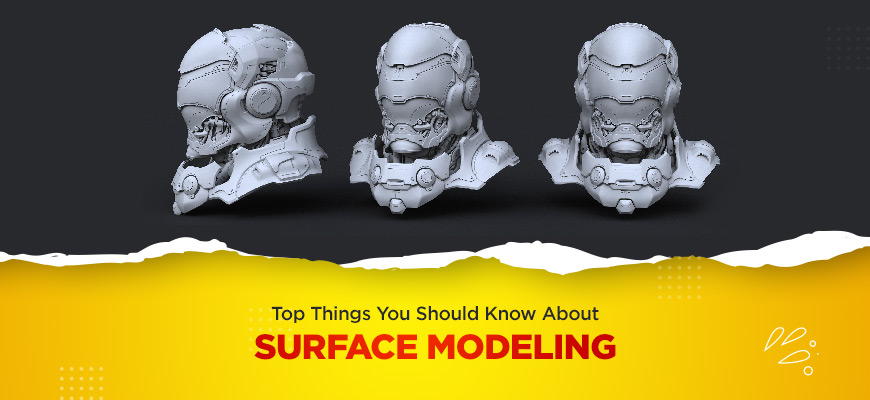
You must have worked with or seen objects with solid appearance in computer-aided design programs. The solid feel is produced with the help of complex mathematical method known as Surface Modeling. With this method, one can visually scan a particular solid surfaced CAD object from chosen angles. Surface modes are mostly used in developing illustrations and architectural renderings.
For architectural designing and rendering, surface modeling techniques is very popular. The method is leveraged for a diverse array of applications like structural part and body panel designing for aircrafts and vehicles, both land and marine.
Compared to wireframe modeling, the techniques used for object display in surface modeling are usually more complex. In this method, the object to be showcased is converted between different 3D modeling variants for a seamless experience. This 3d design surfacing display the functions significantly less unclear than wireframe technique and slightly less complex than solid modeling.
Basic surfacing, which combines both wireframe and surface design can be used while working on solid mechanical parts. However, advanced surfacing or generative surface design is mostly employed by mechanical 3D designers for developing surfaces.
Before we go in depth, it is better that you have a general idea about the 3D modeling techniques, i.e., wireframe, surface, and solid modeling, so that we are on the same page.
What is Surface Modeling?

Surface modeling is a mathematical method of constructing and transforming representations of natural terrains, geometry and surfaces, generated from the 3D information provided. It is usually built from a wireframe model by defining the surfaces. It is mostly popular in industries like architecture, marine vehicle, automobile, and aircraft designing.
Reasons to use 3D Surface Modeling Technique
Ability to create features where algorithm results in division by zero
Often, you have come across a warning like ‘Invalid, Unable to Create Feature’ when issuing command for creating standard features such as a fillet. When drafting between different faces of the 3D models, similar problem sometimes arises.
You would then resort to a different tool or tweaked setting to accomplish the task but despite repeated efforts, you may not experience success.
The reason for this warning, mostly, is the generation of a self-intersecting face or edge when the mathematical calculation would result in an algorithmic deadlock characterized with division by zero. You can easily get around this issue with the help of this modeling technique
- Start by deleting the complex face or edges
- Apply this techniques for reconstructing the complex face/ edge
- Now stitch the newly generated surface to the existing design
You would no longer come across any failure message.
-
Ability to work easily with imported CAD models
If you have imported models from different CAD programs or in third party formats, you have stumbled upon a situation where the feature details of the design are missing. The challenges experienced in altering such geometries are more particularly when the complexity of surfaces is high.
With this modeling technique, you can
- Engage in deletion or replacement of model’s one or more faces
- Make needful changes without any hassle
Related Article : 52 Free CAD Software That You Can Use in 2025
-
Ability to create organic shapes with high level of complexity
On various occasions, you may not be able to generate complex shapes by using solid modeling tools. However, here’s a professional tip for modeling complex shapes with this technique.
Unlike solid modeling, the various facets of the shape are not build at one go with tools for surface modeling. At a time, you can go about building one face only. This helps in controlling the contour and face direction of the organic shape in the exact manner you have desired.
-
Ability to make surface geometries serve as references
When creating surfaces, you are actually building the face of a model. But, direct construction is not the only purpose you can accomplish. Surface built can also double up as reference geometry. This is done in an intermediate stage during building of the desired model’s face.
-
Ability to leverage hybrid modeling methods
When these techniques are blended for the purpose of creation of a solid model, it is known as Hybrid Modeling. In this advanced method, the model is started off as a solid and then surfaces are used for modifying the same. The solid model can also be changed to surfaces for the purpose of shaping and contouring it. Once done, the surfaces are changed back to solid.
Surface modeling can prove to be more difficult compared to solid modeling as you have to work with a single face at one time. But the non-ability to work with several shapes at a time translates into the possibility of creating complex 3D designs which are not possible using solid modeling tools only.
It is crucial to gain expertise of these techniques to enhance your modeling skills to create just anything you want. You need to gain further insights into the strengths and drawbacks of both techniques to be able to leverage any one of them or both to successfully handling different modeling scenarios.
Understanding the strengths and weaknesses of both, enables you to assess which technique will be helpful in a given situation.
Process of Surface Modeling
3D CAD modeling starts with a 2D sketch, and from that sketch, you get two vital options, "surface geometry or solid extrusion", which brings that sketch into 3D. The two models created using these techniques will help you understand surface modeling by comparing it to solid modeling.
We will use the model of a bottle made with surface and solid modeling. The process, as said, starts with a sketch. Using a revolve feature, the first model gets revolved with solid geometry while the second one with surface geometry.
-
Let's start with the shell
The 'Shell' feature is used for the solid model, and 1 mm is the thickness of the shell. To define the open part of the model, the model with its upper surface has been selected. The thicken feature is used for the surface model with a 1mm thickness.
-
The outcome
Even if two different techniques of modeling have been used, the two finished parts are the same. To be efficient and faster with your 3D CAD modeling job, you need to select the best technique of modeling. But here, as we have used the revolve feature, the decision didn't matter. In this case, the focus of the techniques was on different aspects, one being a 3D shape with a thickness and the other one being the thicken feature which has enhanced a 2D curve.
-
Let's move ahead by combining solid and surface modeling
Models cannot be that easily defined using only the solid features; rather, you will have to integrate surface features if you aim to define this complete geometry. There is an organic upper surface in the image which cannot be modeled with solid features.
-
Solid and surface parts defined
The extrude feature is the common solid modeling operation used to define the base of the model. A surface modeling operation known as the "mesh fit" feature is used to generate the upper surface. It shows that a mesh that is a 2D shape is applied automatically to a particular surface.
-
Solid and surface parts combined
The next feature to understand more about is the "cut "feature. It helps in putting both the solid and surface parts together. When the solid model is perfectly cut, the surface model produces the upper part of the result. The elevations, protrusions and the rest of the model are generated using two steps.
-
The final result
The final result shows the importance of surface modeling, without which it is impossible to 3D model a particular part. Understanding both techniques will help you create any model.
If you need help in terms of 3D modeling design services, consider outsourcing to us.
Conclusion
Solid modeling cannot be universally applied to handle the needs of all 3D modeling types. However, to begin with, you must learn all about surface modeling in CAD to consummate your 3D design skills.
That is why make the best use of this article to understand what surface modeling is and then move to the next step. Alternately, you can seek the 3D modeling support of seasoned and proficient professionals of renowned 3d modeling companies like ThePro3DStudio for getting generated impeccable models within low turnaround.
Contact Us